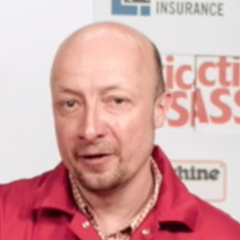
MIG Welding: Little by Little
Ben FieldIt is important not to distort a panel with too much heat, and working gradually toward the end goal is key to a quality finish.
For more helpful tips from Skill Shack, check out our Basics of MIG Welding and Intermediate Welding courses.
Okay. So that's all tacked up now in there. I'm gonna give a bit of a wire brush round, because when you're tacking, you get quite a lot of, sort of, soot around the welds, it can interfere with your runs, when you come to do those. To get that really, really clean again. You can see that's properly held.
I've put the tacks roughly every inch or so, not had my tape measure out to check them, but they are roughly there. So it's held. What you don't want to do, is start doing a weld run and then the panel gets flipped away from where it needs to be. What we're gonna do now is do a series of short runs. I don't wanna put too much heat into this.
And when you're starting to weld, you shouldn't get too sort of ambitious and start running really long welds, because inevitably you'll probably blow a hole. We've got good solid steel here. Got some good solid steel here, but I still suggest short runs. You don't build up too much heat. In some cases you can put some distortion in, if you start to put too much heat in it, in this case, it's so well held here, here, here, and here.
It's not gonna go anywhere. Its not gonna sort of deform badly and afterwards I would go in with a hammer and dolly anyway and sort of dress that up, so it's all in the correct shape. You may be able to see, that here there's some bit of distortion where I've just been knocking the panel and the metal behind, to fit each other, but there was a need to do that and we can dress it up afterwards, once it's all in.
It would have Ben interesting to see what was underneath the new plate.