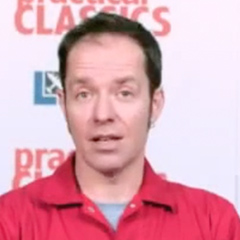
Different Types of Welded Joint and How to Achieve Them
Michael ComanChoosing the correct type of joint for the application is critical for a neat and strong repair. Lap, Joggle, Plug or Butt. Teamed with the correct rust prevention, these can all be used to create a long-lasting repair.
To see more helpful hints, check out our Basics of MIG Welding, Intermediate Welding and Simple Body Repairs courses.
The different ways we can join this. We've got a butt weld, which is probably the preferable way if you've got quite a lot of experience at this way where you butt both of these two panels together and you will put the weld there. You're able to finish that weld off and get a nice flush finish. The difficulty with that is keeping the distortion out of the rear panel. It's difficult.
It's hard work. You've got to take a lot of time over it. It's probably a little bit advanced for us at this time. You can also use a stepped joint. Stepped joint can also be called a joggle or a joddle.
I've seen both of those used. The way that one works, you get a pair of pliers like this that have the step in, in them at the front. And as you clamp them together, you can go round either your repair panel or the car body work, and you would put a step into the metal. So as you go around the metal we'll do this step like that. Or you can put a step like that onto your panel.
The preferable way is to step the car because if you think about it if there's any moisture gets in the back of the panel it will come down and it'll run and it'll drop off there. Whereas if that was the other way around if we'd joggled the panel and the cars was there the water would come down and get right into your joint and start rotting all over again. If you have to do that and you can get to the back of the joint, then you can get away with that. You can seal that. You can prime it and then seam seal it.
And so no moisture gets in. This, on ours, is very, very close so we're not going to be able to do that. The way we're going to do it is we're going to lap weld it. Because we're going to join right in the curve of this panel. That's where a lot of the strength lies in that panel.
We're going to be able to do a small lap weld and then we'll lose that with the weld dressing and also the filling that you're going to need to do afterwards. Underneath the wheel arch we'll put holes in and we'll what's called plug weld that. So you've got a panel with a hole in it and then the other panel underneath, and then you fill that hole up with your weld and that replicates a factory spot weld. And that's what will have happened around here from the factory. They'll have spot welded all that together.
This is very useful, thank-you